Delft Porcelain is a blue and white ceramic made in the Dutch city of Delft. Products made from such porcelain have long become a city symbol and a very popular souvenir among tourists. About the production technology, the history of appearance and interesting facts will be discussed in this article.
History of Appearance
The emergence of Delft porcelain dates back to the 17th century, when pottery in the Dutch city of Delft was experiencing its golden age. One of the main roles in the development of porcelain production was played by the rise of maritime trade. At that time, one of the six representative offices of the East India Company worked in the city, and its ships brought samples of blue-white and polychrome ceramics from the Far East to Holland.
During this period, potters from Delft experienced an acute shortage of clay, so it was brought from other countries. Until 1640, only ten potters could join the Guild of St. Luke (a workshop association of sculptors, painters and printers), whichgave them great advantages.
The increase in the production of pottery was due to the fact that the quality of river water was extremely low. Because of this, the vast majority of breweries closed, and pottery workshops were opened in their place. Also, a large number of breweries closed after a strong explosion of gunpowder stores, which occurred in 1654. A large part of the city was almost completely destroyed.
Demand growth
The need for Delft porcelain was also due to the fact that all goods were delivered to Holland by sea, which was associated with great risk. Delivery of ceramics from China was very problematic, quite often the ships did not reach Holland. Like, for example, a Swedish sailboat in 1745, which hit a rock under water and sank 900 meters from the harbor with a large shipment of porcelain from China. These events also increased the demand for products from Delft craftsmen.
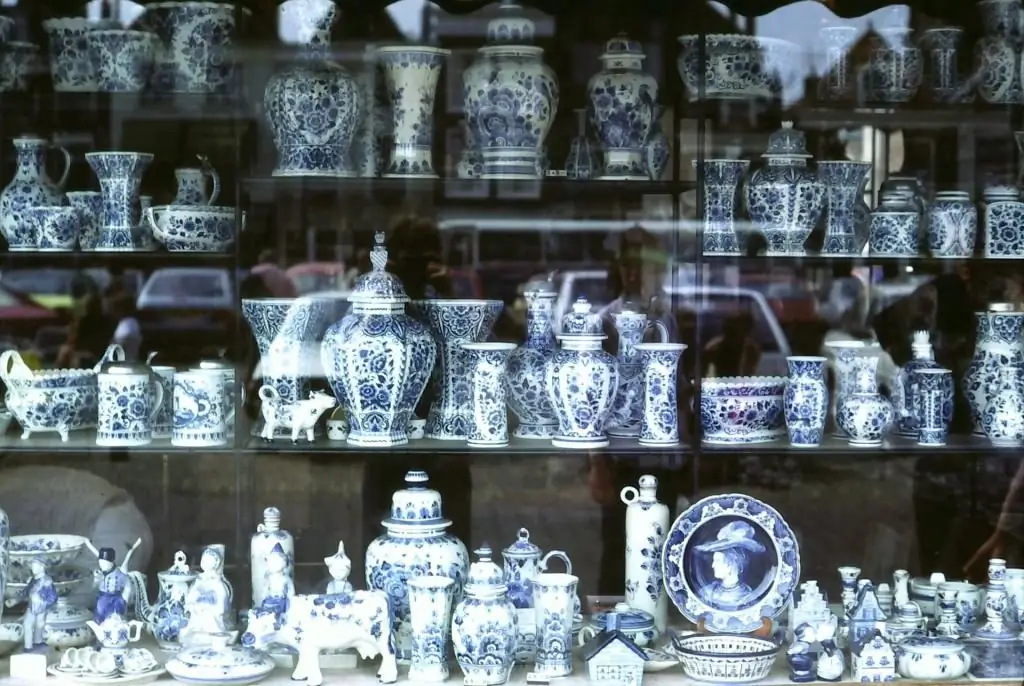
One of the technological features of Delft porcelain was the use of multiple glazing cycles for manufactured products. It was carried out with lead glaze, and the final firing was carried out at a low temperature, which made the product similar in its characteristics to earthenware.
Flourishing production
Porcelain production flourished in Delft from the middle of the 17th to the second half of the 18th century. Delft porcelain was not very durable; they mainly produced tiles that were used to line ovens and walls, as well as tableware and decorative utensils. Initially, the craftsmen copied the shape of the dishes and theirpainting from Chinese samples (ornaments and landscapes of China were in demand). In the future, potters began to produce products with scenes from the Bible and landscapes that are inherent in the expanses of Holland itself (windmills, flower arrangements, fishing boats and the coast).
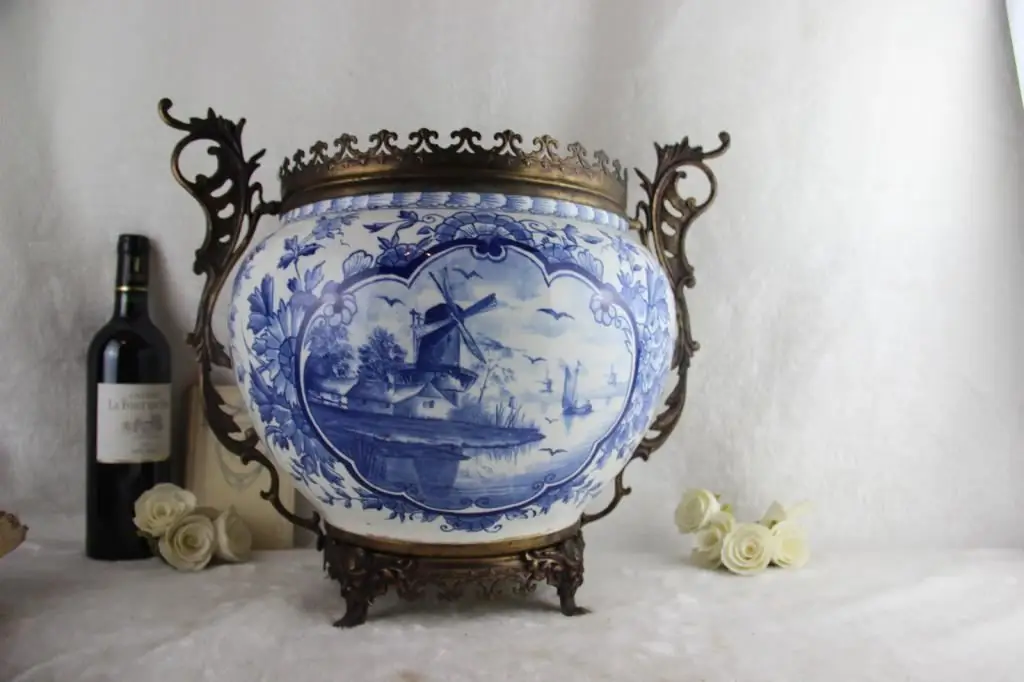
The pattern on the manufactured products was distinguished by its beauty and workmanship, the graceful drawing of thin lines distinguished this porcelain from any other. Since 1650, local craftsmen, in addition to the brand name, put their personal stamp. On Delft porcelain, the brand guaranteed the high quality of the product.
The decline of popularity
Problems with the sale of porcelain from Delft masters began in 1746, when an English chemist, Sir William Cookworthy, invented a recipe for white clay. Dishes and products made from the new material were more durable. The manufactured products were covered with transparent glaze, which gave the pattern depth, volume, brightness and clarity.
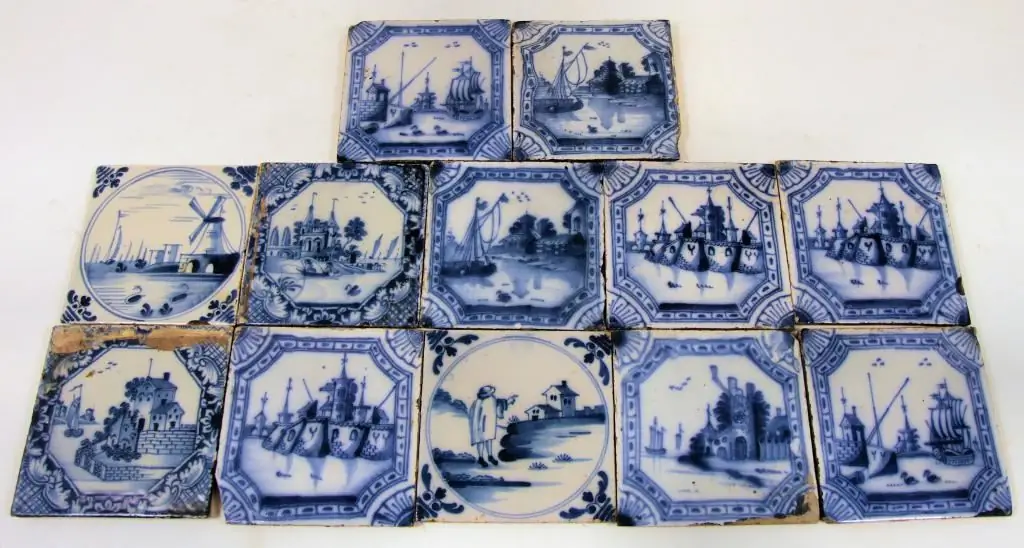
English ceramics were inferior to Delft faience in decoration. For the British, the drawing was not very neat, and the faience itself was rough and hard, the glazed coating cracked and chipped easily. However, English pottery, although different from Delft porcelain, was beautiful in its own way. But its main advantage was its low price, since it was not painted by hand, but by printing.
Dutch manufacturers could not compete with the British, and potters from Delft beganclose their workshops. At the end of the 19th century, only one workshop remained from the flourishing porcelain production. Its owner has kept it because he abandoned the traditional hand-painted products and began to apply patterns in print.
Production technology
At the very beginning of the production of Delft porcelain, plaster molds are taken and filled with a clay solution. Gypsum very quickly absorbs excess moisture, and after hardening in the form, a blank of a future plate, mug or vase is formed. Using a knife, sponge and water, the master separates the remaining seams from the workpiece. Then the future ceramic product is sent to the kiln for 24 hours for the first firing, maintaining a temperature of 1160 ° C.
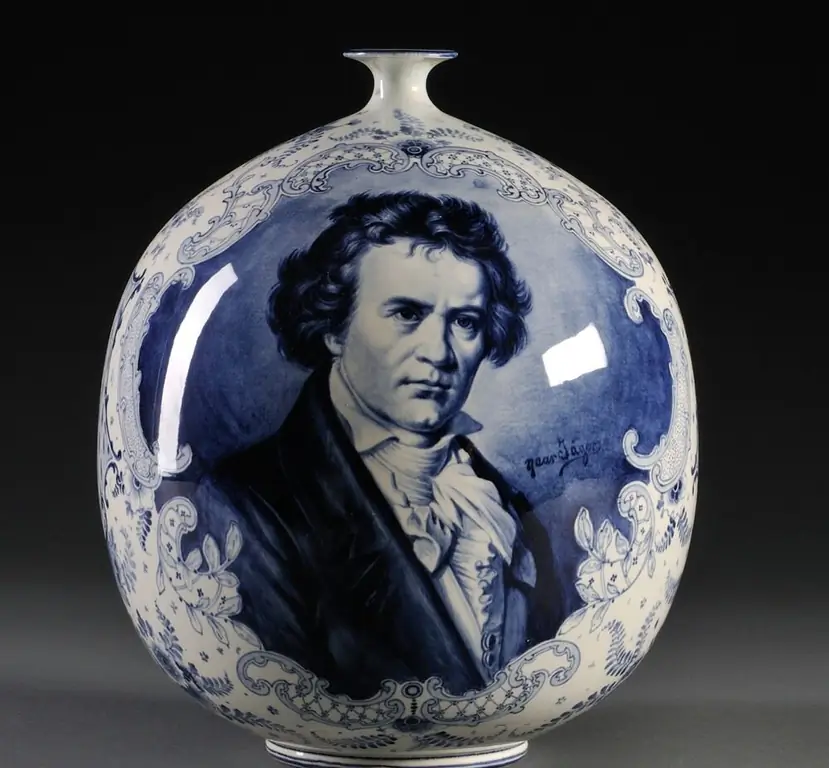
After that, the product, which is called a biscuit, is sent to the artist who paints it. This is the most painstaking and responsible part of the production of Delft porcelain. All products are hand-painted by the master, which is easy to notice, as brush marks remain on the ceramics.
Painting and finishing the process
The paint is immediately absorbed into the porous texture of the clay, so even an insignificant blot cannot be corrected. If, nevertheless, the artist made a slightly sloppy pattern, the product immediately loses its value.
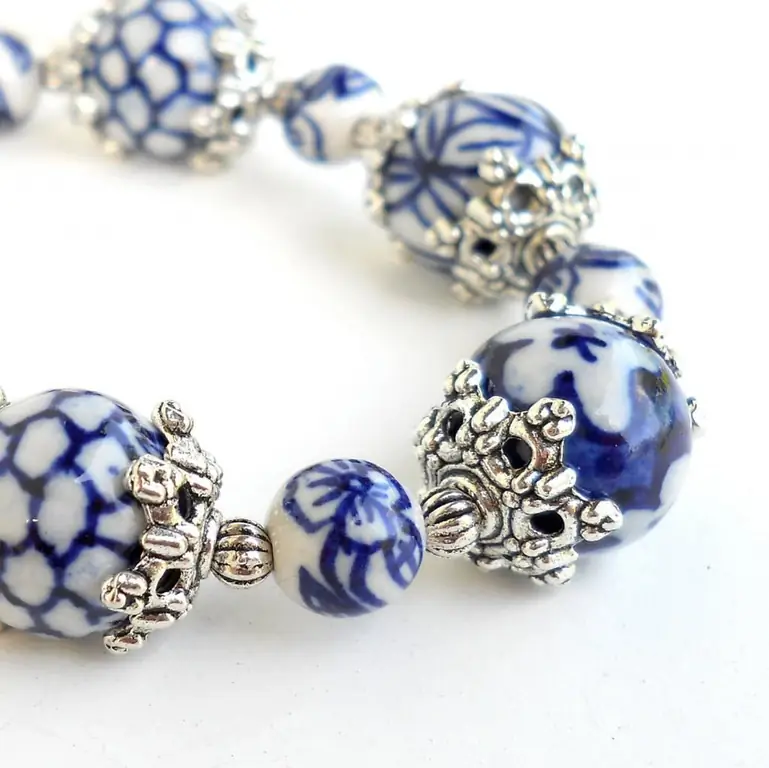
After the product is painted, the pattern depicted on it at first looks bulky and dull. And only after glazing and secondary firing at a temperature of about 1170 ° C, the processconsidered completed. Glaze not only creates a protective layer on porcelain, but also gives the painting a visual depth and volume. In the photo of Delft porcelain, you can see what bright and voluminous patterns are obtained after the completion of the production process.
Keeping Traditions
The secret of making this porcelain could have been irretrievably lost if two Dutch entrepreneurs had not purchased a factory in 1876 to preserve and resume the ancient production of Delft ceramics.
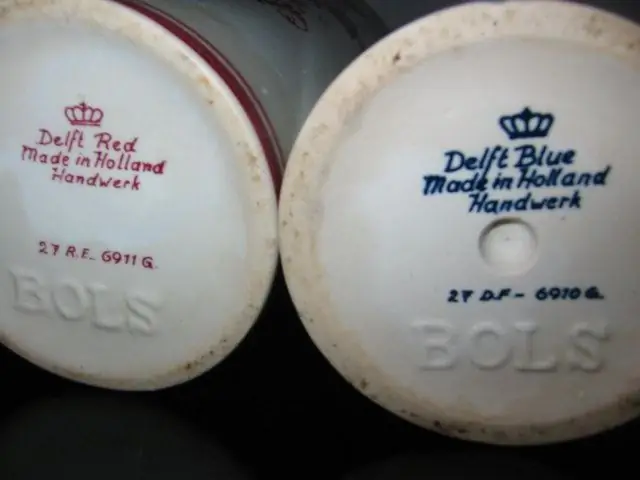
In 1884 they create a new recipe for white clay, which is stronger than English products. Then they completely changed the technological process and began to produce ceramics. Immediately after that, the products began to be a success; in Amsterdam, Delft porcelain was bought up by numerous tourists. This contributed to the growth of recognition of Dutch ceramics around the world.
In 1919, the Delft brand received the title of royal - for the preservation and revival of the pottery traditions of Holland.
Delft Porcelain Factory and Museum
Today, you can see the production process of this magnificent ceramic with your own eyes if you visit the Royal Factory in Delft. In order to attract buyers and maintain demand, it is proposed to look at how Delft porcelain is currently made. Mugs, plates, vases, figurines and more are created in your presence.
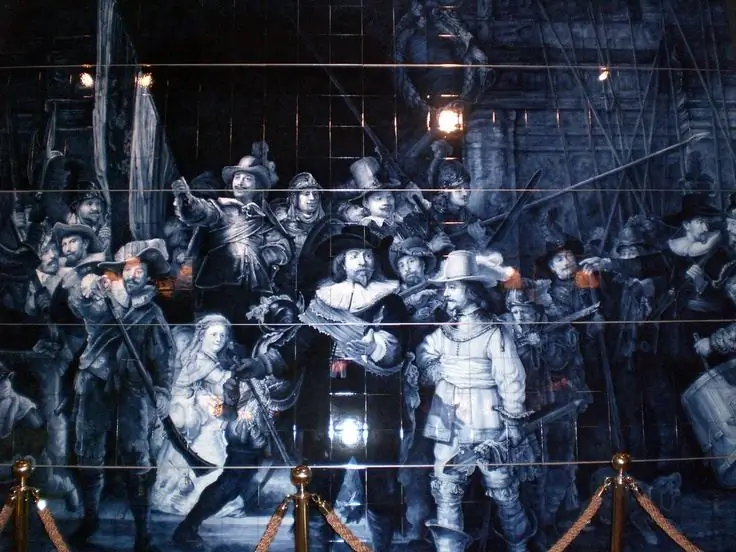
If you wish, you can visit the Porcelain Museum, wherevarious pottery made at the present time, as well as more than a hundred years ago. Some exhibits are real masterpieces, such as a tiled panel, which depicts an exact copy of the famous painting "The Night Watch" by Rembrandt. The whole panel consists of 480 tiles and looks very impressive.
While enjoying the beauties of Holland with its architecture, history and museums, you should definitely get acquainted with the exhibition of Delft porcelain, because it really is a work of pottery art.