Voschina is not just an important component of the high productivity of the apiary, but also a guarantee of the he alth of bee colonies. It is wax raw materials of good quality that can prevent parasites and diseases from entering the hive. And now more.
Well, who builds like that
Perhaps the most intriguing side of the bee colony life is the construction of honeycombs. When forming, restoring or expanding the nest, the wax secretory glands located on the lower part of the abdomen begin to function in the bees, and the colony builds new combs. According to statistics, one bee family produces up to 7 kg of wax per season. In cultural beekeeping, artificial foundation is used to activate and speed up the process. This allows you to solve a huge mass of problems that beekeepers of past centuries often faced. The undeniable advantages include:
- Bees build only straight vertical combs.
- Greatly reduced the number of drone cells.
- The number and quality of the brood of worker bees and, consequently, the commercial yield of honey are increasing.
The inventor of the artificial basis for building honeycombs is considered to be JohannesMering.
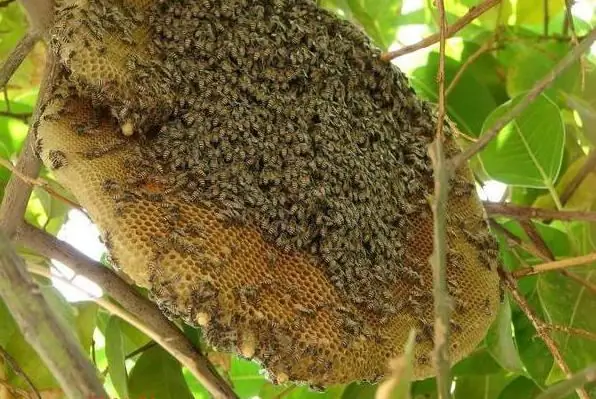
History of Creation
In 1857, a German beekeeper from Frankenthal, observing how women deftly use waffle irons to form and then bake treats, had the idea to apply a similar technology to make wax with their own hands. Having made a similar device out of two boards, Johannes set the matter on stream, independently printing the volumes of flat sheets of honeycomb he needed.
Four years later, S. Wagner improved Mering's products. He found a way to draw on the leaf a pattern of the base of the walls for future combs, which significantly reduced the tuning time and the energy expended by the bees. Wagner used elementary rollers with the appropriate texture for this. The wax sheet became stronger, but was still very rough. In the following decade, several inventors proposed their own versions of foundation rollers.
From handicraft to industrial
In 1876, the joint efforts of the American entrepreneur A. I. Ruth and the outstanding engineer A. Washburn allowed them to create an almost perfect rolling machine. An alternative production option could be the use of presses. But the Given mechanism released in the same year was not widely used. Slightly more successful was the Ritsche press with foundation dies, which, although it was in good demand in the European markets, had a significant drawback - wax gradually accumulated in the bottoms of the cells.
Almost until the end of the XΙX century, the mainThe wax production method was dipping: a thin board was alternately immersed either in a melted wax mass or in cold water. To obtain a uniform thickness of the sheet, the board had to be rotated. Finally, in 1895, a machine was designed (by E. B. Weed) that rolled wax sheets of any length with perfectly uniform output thickness.
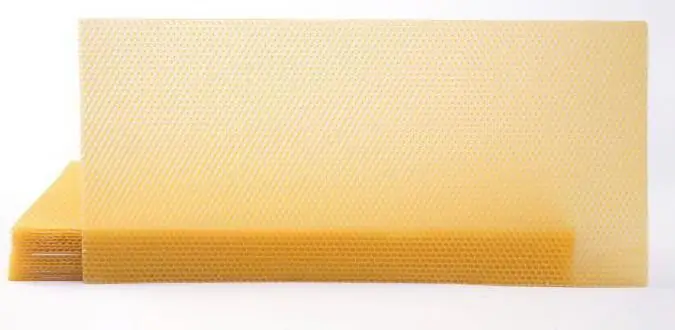
Modern equipment
Current foundation production is a full high-tech cycle, including several operations - from thorough cleaning of raw materials to packaging of finished products.
First of all, the incoming raw material (dry land, merv, render) is separated from impurities. After grinding and heating to melting, the hot mass is poured through strainers into a storage tank. After settling and separating suspended impurities, the preparatory process is completed by heating the wax to 120˚C. This is necessary for the destruction of parasites and pathogens.
The next step is to get a smooth wax tape. The molten mass at a temperature of 75-80˚C is fed to the surface of rotating drums cooled by running water. The resulting wax plates (thickness about 5 mm) are separated from the surface with a special knife and sent for further rolling. By adjusting the angular speed of the drums and the temperature of the cooler, the resulting material is rolled several times. At the output, a smooth tape is obtained, with a thickness of 1 to 1.5 mm. In a receiving bath filled with water, at a temperature of about 20˚C, it is wound into a roll.
Basic operation -double-sided embossing of a honeycomb pattern on engraving rollers coated with a fairly soft tin alloy. The resulting texture tape is cut with a mechanical knife in accordance with the size of the frame. The foundation has a standard size of 410 × 260 mm. On average, it takes about 1 kg of wax to make 15-16 sheets.
At the final stage, the sheets enter the drying cabinets. After removing excess moisture, the foundation is packed and sent to consumers.
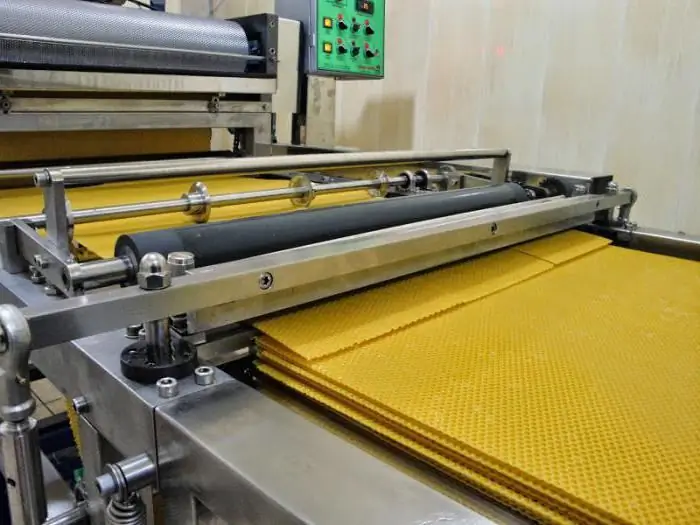
Product types
Industry produces three types of products. Depending on the sheet thickness and weight, foundation is divided into:
- Shop. The thinnest piece. It is used for waxing magazine and reduced body frames when expanding the family, as well as for the production of comb honey.
- Nested. There can be from 16 to 18 sheets in a kilogram of foundation.
- Reinforced. This three-layer or steel-wire reinforced foundation is slightly more expensive than nested foundation, but has good density and resistance to thermal distortion.
Wax Plus…
Until recently it was believed that foundation is a natural product made only from natural raw materials - wax. But in recent years, the term "artificial" has received a completely new interpretation. This is the name of the product, which, in addition to wax, includes other ingredients. The most common additive is paraffin. The cost of foundation is certainly decreasing, but at the same time the quality suffers - the strength of the sheet is noticeably reduced.
And finally, in somecases in the manufacture of foundation, wax is not used at all. The main components are plastics and paraffin. Unnatural foundation is easy to distinguish by smell, texture and color (to give an attractive look, it is specially tinted in bright colors). For use in the apiary, such sheets must be covered with a thin layer of wax before installation in the hives.
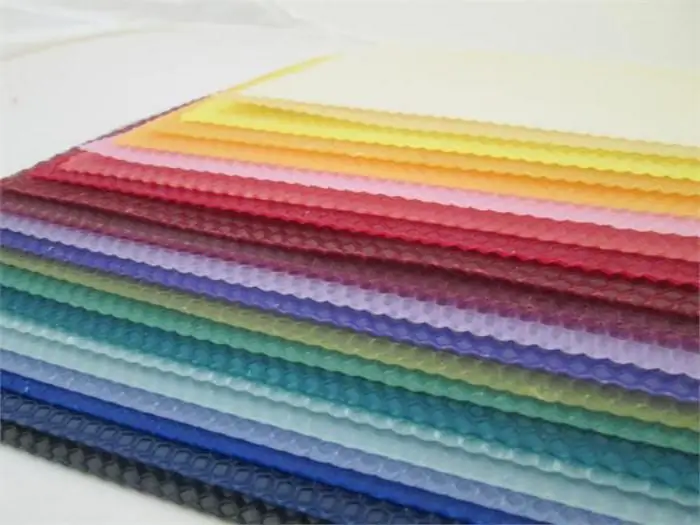
Comb for drones
Many beekeeping farms pay due attention to the extraction of the most valuable and unique beekeeping product - drone homogenate (milk). This is a specially collected and processed mass of drone larvae. Drone foundation is used to increase the yield of products. It differs from the traditional one in the size of the base of the cells increased to 7 mm. The sheet itself is also thicker and more durable.
In addition, to limit the egg laying of the uterus and increase the commercial yield of honey, drone wax is sometimes used to make store frames. Such sheets are actively used in breeding work and in the fight against varroatosis.
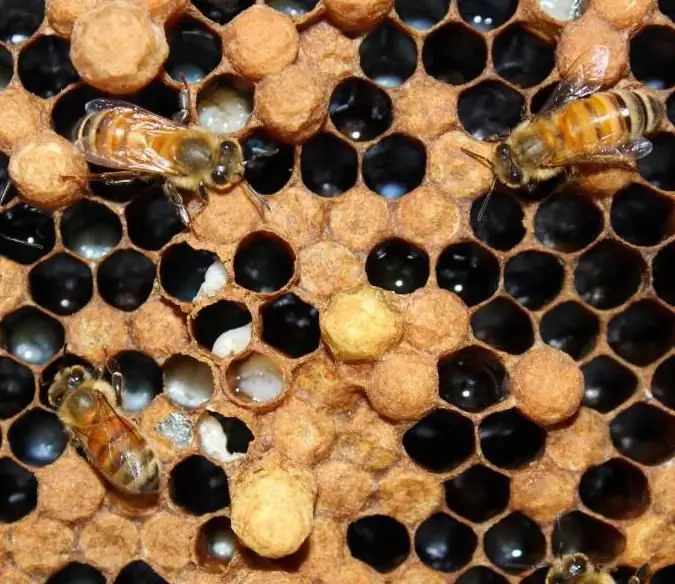
The problem of choice
The well-being of the apiary largely depends on the correct choice of foundation. Even a careful visual inspection can tell a lot about the quality of the product and the integrity of the manufacturer. The first thing you need to pay attention to is that the sheets should not have damage, dirt or foreign inclusions. The foundation must strictly correspond to the size of 410 × 260 mm (410 × 190 mm for multi-hull hives) and be transparent to the light. Cell bases - haveregular hexagonal shape with strictly parallel sides. All should be the same size (5.3-5.5 mm). It should be noted that for Asian bees the indicated parameter is somewhat less - 4.3 mm, i.e. there will be more cells on the foundation sheet.
Packaging and storage
For the convenience of counting the remaining foundation stocks in the apiary, the sheets are packed in bundles weighing 1, 3 or 5 kg. According to GOST 21180-2012, the packaging must indicate:
- manufacturer and its location (postal address);
- composition and product name;
- packaging date, shelf life and storage conditions;
- net weight, number of sheets.
Packages are placed in plywood boxes and are allowed to be transported by any means of transport. Packs are recommended to be stored at a temperature from 4 to +30˚С in dry places inaccessible to rodents. When choosing a room, it should be borne in mind that wax absorbs odors well. The height of storage of packages should not exceed 0.6 m.
Decorative and applied value
Natural foundation is the most fragrant natural material. It is very popular with home craftsmen. The uniqueness of foundation lies also in the fact that it is hypoallergenic and you can safely work with it, and any person, even predisposed to allergies, can use the products. Sheets are often used to make decorative flowers, flat figures. But wax candles are the most widely used.
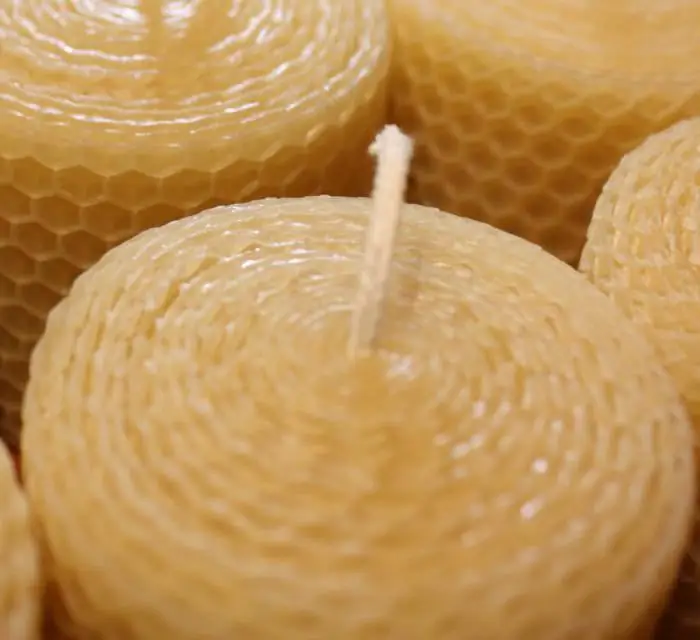
Scent of burning candlesnot only gives spiritual harmony, soothes and promotes deep restorative sleep, but also purifies the air in the room, serves as a wonderful antiseptic. Just two hours of daily aromatherapy - and within a week the healing effect will be noticeable.
The so-called rolled candles are made from thin sheets of foundation. They have been known to mankind for a long time - traditions and skills are passed down from generation to generation from ancient Russian beekeepers and beekeepers. Sheets are selected whole and without visible defects and contamination. Otherwise, the product may simply crack, burning will be unstable and uneven. You can make a candle from a standard foundation, with a diameter of about 3 cm and a height of up to 26 cm. No special tools and devices are required for manufacturing - a well-heated sheet is easily twisted.
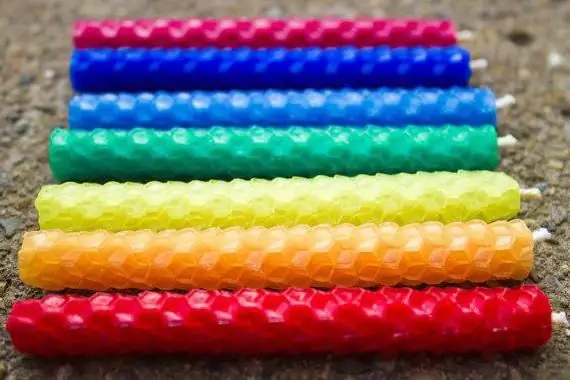
A few words about the central element of the wax candle. The wick is woven from a thin cotton thread. Its thickness depends on the diameter of the product. The following ratios of diameters are considered the most optimal: candles up to 30 mm are equipped with a wick 1.5-2 mm, up to 50 mm - 4 mm, up to 65 mm - 6 mm. For more solid products, a wick with a diameter of 10 mm is used. The end of the thread should protrude at least 5 mm above the top of the candle. To facilitate ignition and give an aesthetic appearance, it is impregnated with wax.