Flanged valve is installed on pipelines to provide the ability to quickly shut off the liquid supply and subsequent dehydration of the medium. To increase the level of security, these elements are located in all parts of the network.
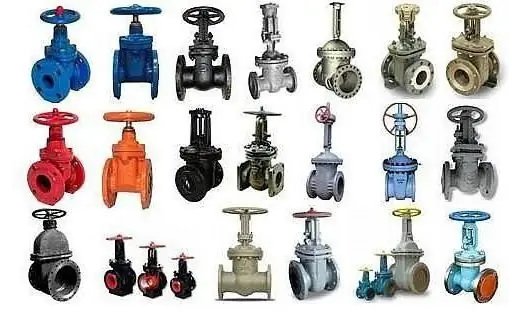
Description
Flanged gate valve acts as a shut-off valve and has a simple design, despite the high efficiency. It belongs to the category of shut-off household taps and has a special blocking part in the center of the structure, its execution depends on the type of valve itself. The most widespread are disk locking, wafer wedge and ball rotary elements.
The flanged valve got its name due to the special flange rings located at the edges. They are used to provide quick access to the system and the ability to remove the fixture for replacement or repair work. It is worth noting that the dimensions of the mating flange element must correspond to the main plate. Otherwise, the connection will not have the proper quality, or it will become impossible at all.
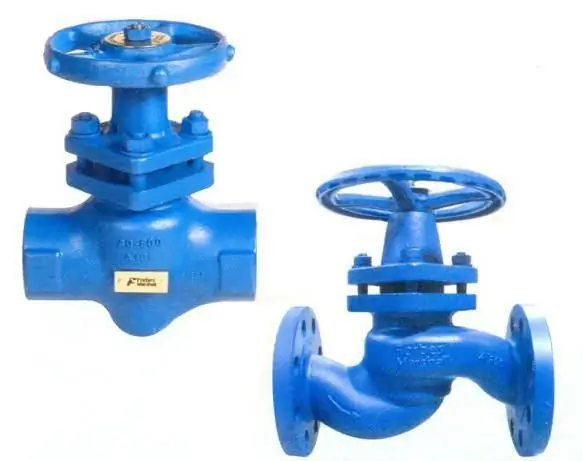
Pros and cons
Among the main positive aspects, it is worth noting the following:
- ensure the ability to quickly repair or replace the device with a new one;
- simple design;
- long service life;
- low hydraulic resistance;
- reliability.
The main disadvantage is the large mass. This leads to a high cost of elements, especially large-sized ones, since a large amount of material is needed for their manufacture. Also worth noting is the rapid wear of the seals.

Varieties
The cast iron flanged gate valve is available in various versions. Devices are divided into types according to the direction of action - parallel and perpendicular. The latter option is stationary and extends perpendicular to the main flow. Parallel attachments mount at zero angle and are not obstructive to flow when in standard mode.
There is also a division according to design features - these are gate, ball and wedge-shaped elements. The latter are shut-off valves of a standard type. They are quite effective, have a perpendicular type of blocking, but are heavy.
The ball-and-socket design is similar to locking household elements of a similar type. The most widely used devices are DU 50 due to their relatively low cost. gate valveflanged DN 100 has a special disc element that closes the pipeline with a powerful spring. As a rule, it is installed on oil pipelines and gas networks.
Classification by management method:
- Handheld devices. This type is controlled manually by turning a special handle or valve. Although they require considerable physical effort, they require no maintenance and rarely fail.
- Electrically actuated fittings. It has a built-in electric motor for control. The system is locked autonomously, after pressing the button.
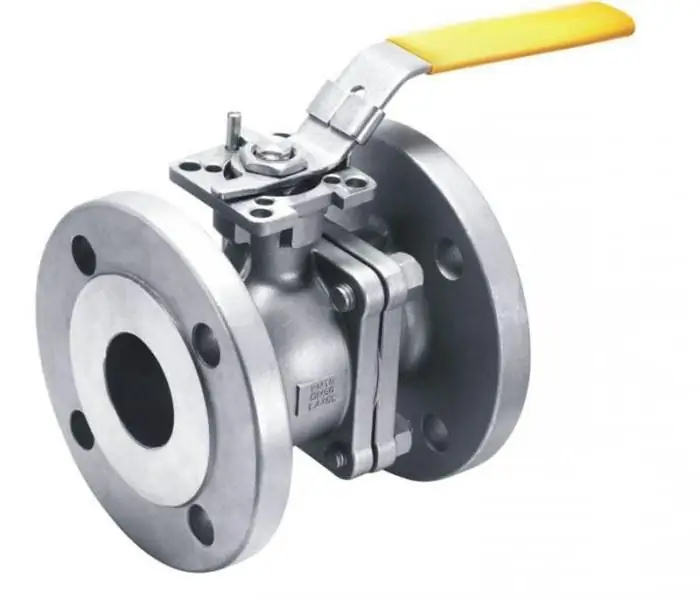
Working conditions
Flanged valve operates in various pressure ranges, the maximum level can reach hundreds of units. The operating temperature ranges from +200 to -50 degrees. Cast iron parts are characterized by extended characteristics, in particular, work with gaseous substances can occur at +400 degrees, and the transported liquid medium can have a temperature of +270 degrees Celsius.
Clinker flanged gate valve is mainly produced from materials such as cast iron and steel. This parameter is located in the label of the device. Any products equipped with flanges must be carefully selected according to the dimensions, which are regulated by special documents. First of all, the diametrical size of the conditional passage is taken into account. If there are any inconsistencies with this criterion, the connection becomes impossible. If used for installationflanged steel product with a size of DN 80 or DN 50, the flange going to the adjacent pipeline must have the same parameters. At the same time, the flanged gate valve, the retractable spindle of which performs rotational-translational movement during opening, can be produced in various sizes. The maximum size can be up to 1500mm, the smallest rebar has a diameter of 25mm.
Scope of application
Elements DN 80 and DN 50 are most widely used in secondary pipelines and side branches of systems. In addition, they are used on large domestic systems, branches and in boiler rooms. The flange valve 100 is much larger and is installed on the main heating and water supply pipelines. DU 200 products are used only in industrial conditions on pressure main systems, while large special bolts are used for their installation. The cost of fittings depends on both dimensions and design features. The price of the material used in the manufacture also matters.
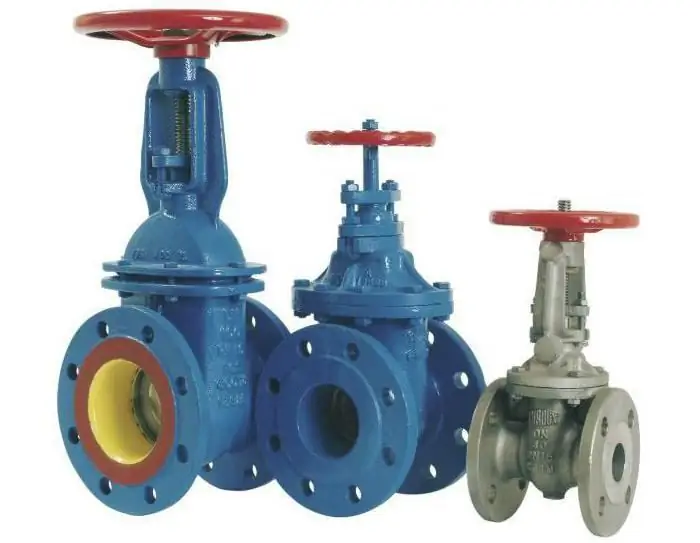
Installation
Installation of products is carried out according to the standard scheme. At the same time, work is simplified by welding flanges to pipes or valves. Otherwise, the workers would have to independently connect the valves with additional parts and weld individual pipe elements. This process requires large financial and time costs, and is also characterized by some difficulties, the failure of which canlead to problems during operation. This is of particular importance in the industrial sector.
With the help of a sealing rubber ring element, tightness is increased. It is installed in a channel located on a flange plate. On the front side of the plate there should be no scuffs and any other damage, otherwise there is a possibility of depressurization and a breakthrough of the system. Under the condition of working with high pressure pressure, this is fraught with serious consequences.