Mostly knives are made of steel. But sometimes craftsmen use other materials to make cutting tools. Often on the shelves of shops you can see sets of ceramic and wooden knives. Such blades have their own special purpose.
On the market, they are presented in a fairly wide range. Those consumers who want to save money or like to craft can make them themselves. Information on how to make a wooden knife with your own hands is presented in the article.
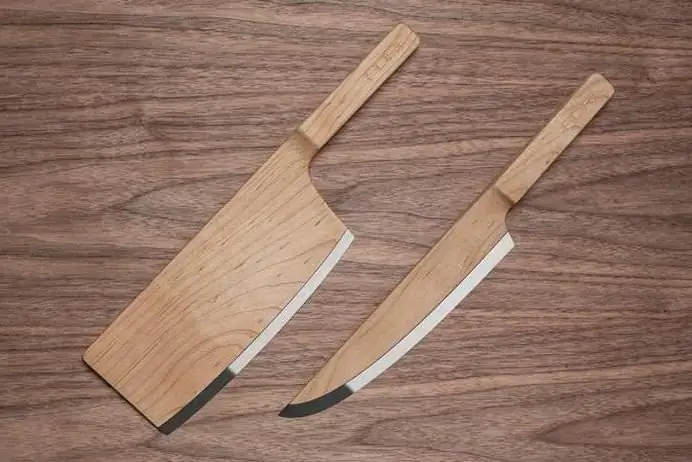
About the purpose of the product
Modern kitchen utensils are equipped with a special non-stick coating. Such dishes will last a long time if the owner is as careful as possible during its operation. To do this, you have to work with such inventory only with certain cutlery.
One of them is a wooden knife. It can be used with modern pans and pots without fear ofdamage their non-stick coating. Unlike similar products made of glass, plastic and silicone, a wooden knife is considered environmentally friendly. It is mainly used for cutting minced meat.
The need for such a product of some thrifty consumers makes you think about how to make a wooden knife yourself. Unlike a classic blade made of metal, making a knife from wood is much easier: this procedure is less laborious. Knowing the technology, you can create quite good wooden knives. Photos and instructions for making such products are offered below.
What do you need for work?
To make a wooden knife with your own hands, the master cannot do without the following tools:
- wooden mallet;
- saws or jigsaws that will be needed to cut the workpiece;
- pencil;
- chisels;
- carving knife;
- sandpaper;
- one block of wood.
The first thing experienced craftsmen do is prepare a wooden block. The workpiece must be thoroughly cleaned of bark. You also need to have an idea of what the design of a wooden knife should be. After the master has decided on the size and shape for the future product, a drawing is applied to the surface of the bar.
What to do next?
After the contour of the knife is outlined on the bar, you should walk along it with an electric jigsaw or saw. The workpiece cut from the bar must be carefully sharpened. The shape of the knife is improved with the help of a woodenhammer and chisel. Using these tools, craftsmen give the product the desired sharpening. In this case, it is recommended to take into account the location of the wood fibers, and it will be possible to prevent chipping if you cut along the fibers.
Shutting down
The resulting knife should fit comfortably in your hand. The final stage is the careful processing of the surface of the product. For this, sandpaper is used. According to experienced craftsmen, grinding should begin with coarse-grained emery. And at the very end, the wood is polished with fine-grained sandpaper.
About application
The purpose of such a knife is one - it is cooking. Therefore, it is undesirable to apply paints and varnishes to the surface of this product, as this may adversely affect the taste of food. During the frying of meat, the knife will constantly come into contact with vegetable oil, which over time will penetrate deep into the wood fibers. Therefore, it is desirable to use the product for cooking one dish.
Plywood product
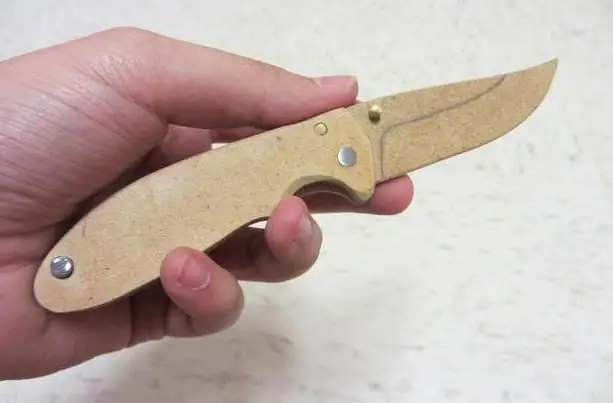
To work, the master will need a sheet of plywood. It needs to be divided into three parts. On each of them, drawings of the details of the future knife are applied. On one piece of plywood, draw the shape of the entire product, and on the other two, only the shape of the handle.
Using a jigsaw, all three elements are carefully cut out. The resulting two stencils with the image of the handle must be applied on both sides to the first stencil - with the image of a knife. Then using metal pinsor other fasteners, all three parts are connected to each other.
The resulting product can be further painted and varnished. Such a knife is considered a souvenir. You can use it as a decoration, not a kitchen appliance.
Gift option
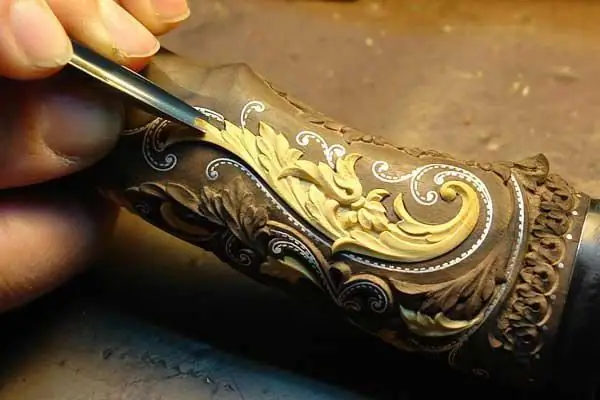
According to experienced craftsmen, a beautiful and durable wooden product can be made from linden, cherry and ash. You need to start with a sketch. The master must calculate what size the blade, handle, guard and crossbar will be - one of the important elements in the design of a hunting knife that separates the cutting part and the handle.
After the sketch is ready, a blank is cut out of the solid wood using a circular saw. The product is shaped by hand. For this purpose, a regular or special knife is suitable. The second option is preferable, since such a blade is an oblique blade, which is very convenient to work with.
The central part from the blunt end of the blade must be equipped with a special hole. A mounting pin will be inserted into it. Using the sketch, the master also makes a guard. The material for this element will be a separate board.
The guard is cut with a jigsaw. It also has a drilled hole for the mounting pin. After that, the guard should be put on the blade. For the handle of a hunting knife, a tree of any breed is suitable. If the master plans to make a round handle, then it is advisable to use a lathe for work.
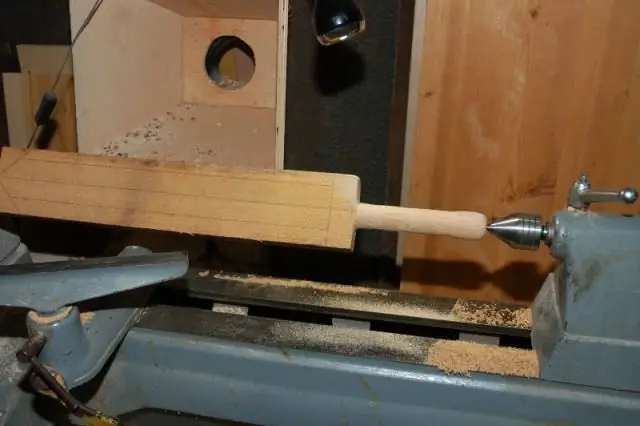
According to some owners of such products, a wooden homemade knife will be much more comfortable to hold in your hand if its handle is made flat. After processing on a lathe or with a chisel, a hole is drilled in the handle for the mounting pin. Its diameter should match the hole in the blade itself.
Now the knife is ready for assembly. At this stage, the craftsmen use a pin and wood glue. When it dries, the product is carefully sanded with sandpaper. Such a knife will look much more spectacular if it is varnished.
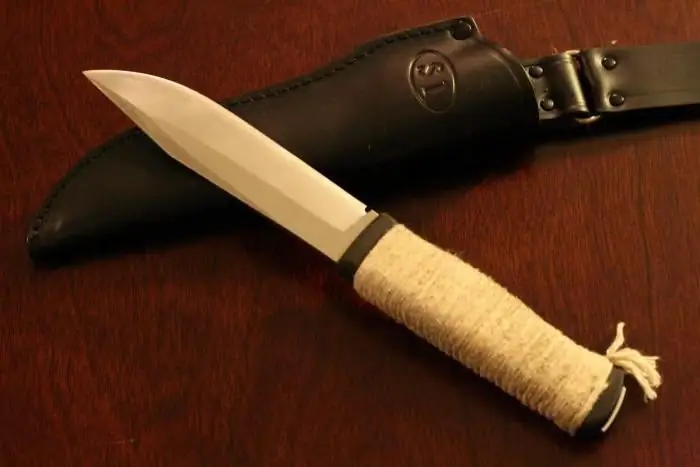
Many masters put beautiful drawings and monograms on the handles of their products. In addition, some stick leather appliqués on the handles. For comfortable carrying, real, made of steel, hunting knives are equipped with sheaths. You can use this and sew a similar device for a fake product. Put in a case, the wooden knife will look like a real one.