Thin steel is used to make a variety of designs. At the enterprises, welding work is carried out using special devices that provide products with an optimal connection. How to cook thin metal with an electrode at home? What equipment works best? These are the questions asked by inexperienced welders who are forced to work at home. You will find information on how to weld thin metal with an electrode in this article.
What are the difficulties?
The importance of the question of which electrodes are best for welding thin metal is due to the fact that if they are chosen incorrectly or if the rules of work are not followed, the master may have problems. These include the following:
Due to the fact that you have to work with a fairly thin material, it is important to correctly calculate the current strength. Otherwise, several through holes may form in the metal. They are also the result of slow suture guidance
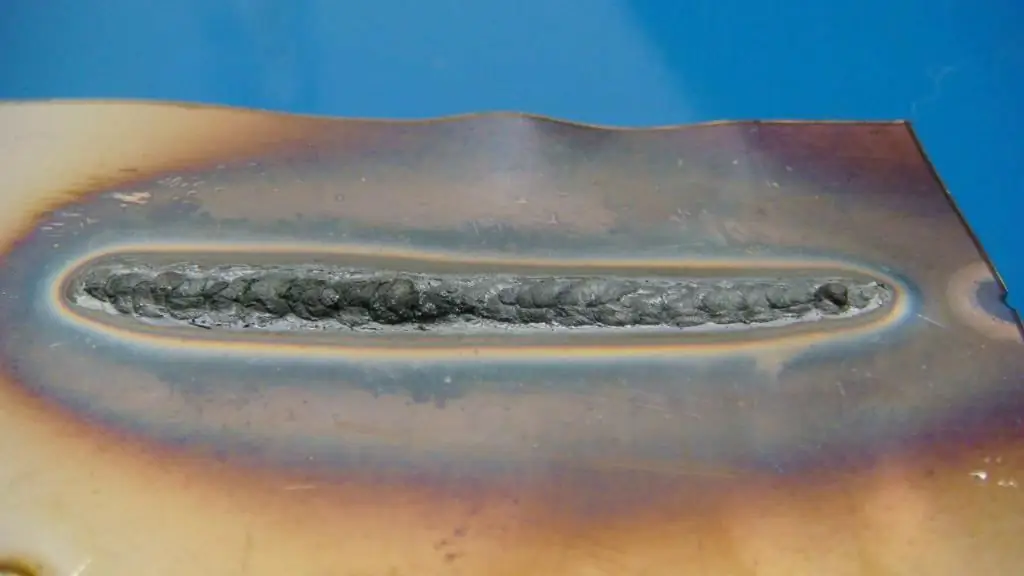
- In an effort to prevent burns,many welders are in too much of a hurry to go through the joint. As a result, an unfinished place remains on the treated surface. Specialists call such areas lacks penetration. As a result, the connection is obtained with poor tightness, and the product is considered unsuitable for working with liquid. In addition, the metal has a low tear and fracture resistance.
- Often, those who do not know how to weld thin metal with an electrode make another mistake, namely, they leave sagging on the back of the connected products. If the front side of the surface looks normal, then the back leaves much to be desired. You can prevent this with the help of special substrates. It is also desirable to reduce the amperage or change the welding technique.
- It happens that the design is deformed. The reason is overheating of sheet steel. Since the metal structure remains cold at the very edges, and the intermolecular component expands at the point of welding, waves begin to form on the surface of the steel, which leads to a general bending. According to experienced welders, the problem is solved by cold straightening - with the help of rubber hammers, the sheet is straightened. If this is not possible, then you will have to correctly alternate the suturing during welding.
To prevent these shortcomings, you need to know how to weld thin metal with an electrode.
About current sources
For welding, such sources can be transformers and inverters. According to experts, the first option is now considered obsolete and will soon be abandoned. Despite the presence of undeniable advantages (high reliability and endurance), transformers squander the power grid too much, which often leads to damage to wiring and electrical equipment. Inverters, on the contrary, do not plant the network and, according to experts, will be an ideal option for a novice welder. If earlier, when working with a transformer source, the electrode stuck to the surface and burned the network, then with an inverter source, the welding current simply turns off. At the very beginning of the ignition of the arc, a current surge is observed on the transformer, which is undesirable. The situation is different with inverters - in these devices, due to the presence of special storage capacitors, the energy pumped earlier is used.
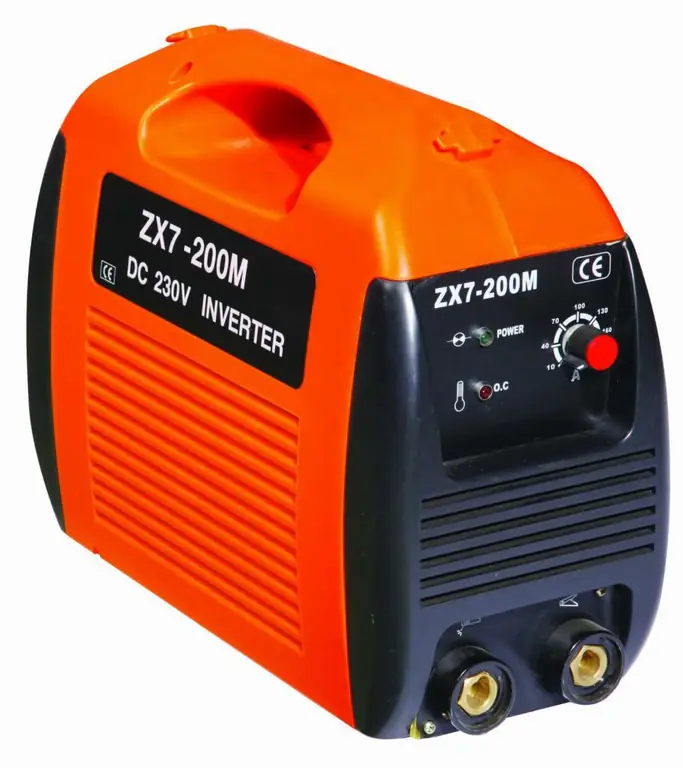
About arc welding
According to experienced craftsmen, the success of arc welding depends on the quality of calcination of consumables. The optimum temperature is considered to be 170 degrees. In such a thermal regime, uniform melting of the coating occurs. At the same time, it is convenient to manipulate the arc, forming a seam. Welding electrodes for thin metal sheets must be with a high-quality coating. In accordance with the technology, an intermittent arc is formed by short-term separation from the electrodes from the weld pools. If the product has a refractory coating, then a kind of “visor” will necessarily form at its end, which will interfere with contact and the creation of an arc.
About the cross section of electrodes
According to experts, the power of the output current directly dependson the diameter of the electrode. A thick one will require a source that can provide a large amount of current. Thus, for a certain diameter, a specific power indicator is provided, beyond which it is impossible to go.
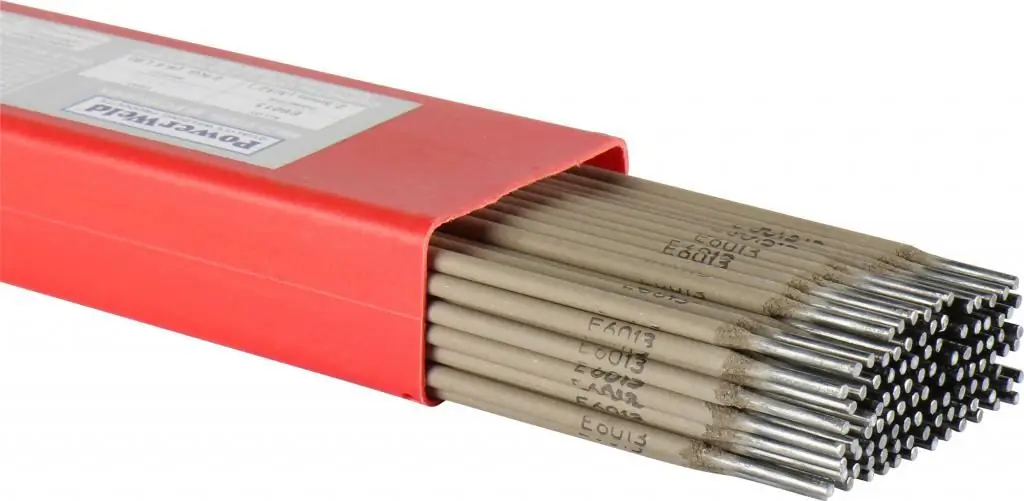
If it is deliberately underestimated, then the weld simply does not form. Instead, only metal streaks with slag and electrode coating will remain on the treated surface. For example, if you work with a 2.5 mm electrode, the minimum current should be 80 amperes. Up to 110 amperes, it is overestimated when they work with an electrode 3 mm thick. Judging by the numerous reviews, the idea to perform welding with electrodes with a cross section of 3 mm at a current of 70 amperes is initially a failure, since no seam will work.
Where should I start?
Before you cook thin metal with an electrode, you need to choose it correctly. Due to the fact that you will have to cook with a lower voltage, it is not advisable to use 4-5 mm electrodes. Otherwise, the electric arc will "stall" and combustion will not be carried out to the fullest. What electrodes to cook thin metal with an inverter? Judging by the numerous reviews, electrodes with a thickness of 2-3 mm will be the best option.
What do experts advise?
Those who do not know how to weld thin metal with a 2 mm electrode should use a special calculation table. For material whose thickness does not exceed 1 mm, apply a current of 10 A and 1 mmelectrodes. Judging by the numerous reviews, they burn out quickly enough. If you have to work with a metal of 1 mm, the current strength should vary from 25 to 35 A. For such welding, you will need electrodes with a cross section of 1.6 mm. 2 mm are recommended for sheets with a thickness of 1.5 mm. The current strength indicator in this case is higher and amounts to 45-55 A. For metal 2 mm thick, electrodes with a cross section of 2 mm are provided. In this case, a current of 65 A is used. How to weld thin metal with a 3 mm electrode? As experts recommend, a product with such a cross section is used to work with metal 2.5 mm thick at a current strength of 75 A.
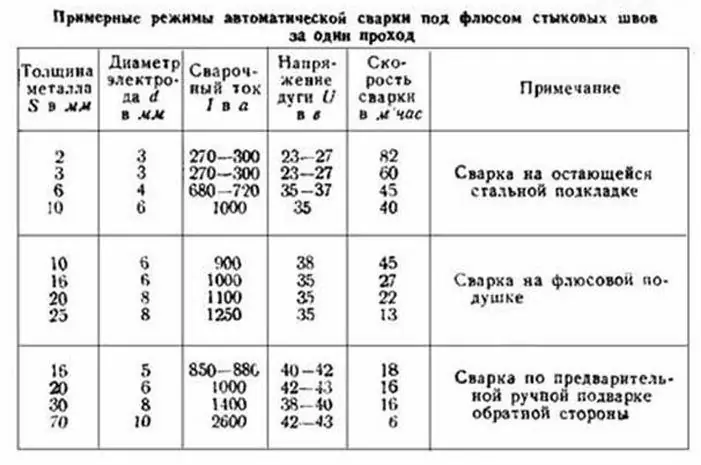
About butt joint
Due to the fact that thin-sheet steel sheets are joined in a joint, the material is often burned through. To prevent this, you need to correctly bring the edges of the plates. Most welders prefer overlapping plates. In this way, a base will be formed for the weld metal, preventing it from burning through. Nevertheless, many beginners are interested in how to weld thin metal with a 3 mm electrode in a joint? As experienced welders recommend, when placing plates, it is not necessary to cut their edges. There is also no need for a gap between them. It is enough just to bring the ends of the sheets to be welded closer to each other and carry out their tacking. It will be easier to work in the low current mode and with the help of relatively thin electrodes.
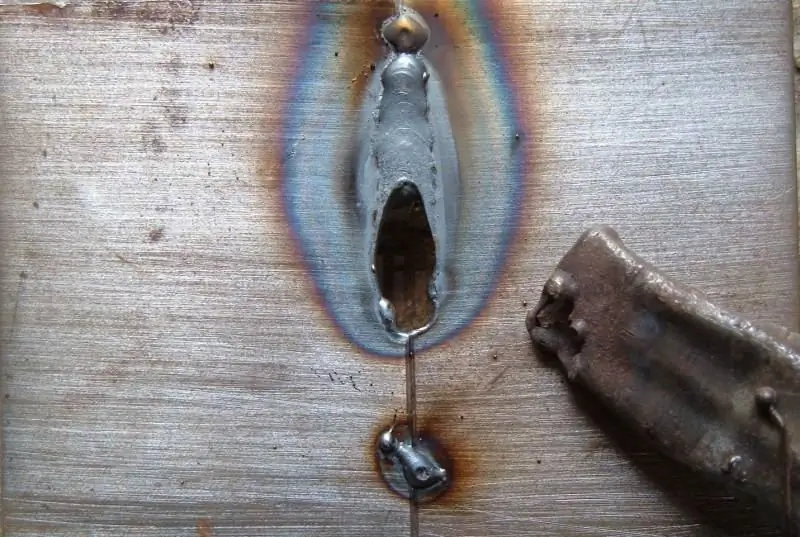
Ohbutt welding methods
Butt welding is carried out in several ways:
- First, the unit is set to low mode. The formation of the seam is carried out quickly and clearly along the joint line. It is not necessary to make oscillatory movements in this case.
- This method uses a slightly increased current. To form a seam, it is recommended to use an intermittent arc. This measure is due to the fact that to give the material time to cool before a new "portion" of additive is applied to it.
- The third method is almost the same as the previous one. However, in this case, welders use special substrates, the task of which is to support the heated area and prevent it from falling through. Judging by the reviews, it is undesirable to use a metal table as such a substrate. Otherwise, it will simply weld to the product itself. The best option would be a graphite lining.
- Some craftsmen practice staggered welds. This method prevents deformation of the structure. You can also place the seams in small areas. To do this, a new seam begins to form from the point at which the previous one ends. Through this method, the product is evenly heated, preventing its deformation.
Progress of work
Before welding, the parts to be joined are carefully cleaned of rust. Units that provide direct current are good because you can use reverse polarity for welding.
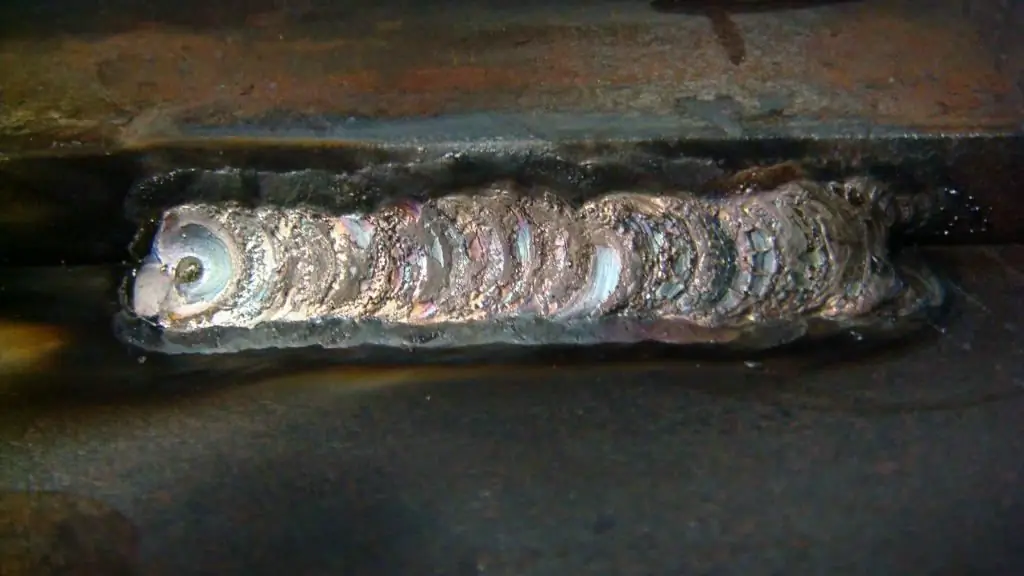
It is enough to insert the electrode into the holder, which is connected to the cable with the “+” designation, and the cable with the “-” to the surface of the steel part. This method of connection will provide a large heating of the electrode, and the metal surface will warm up less. If the master aims to heat the connected products weaker, then they must be placed vertically. According to experts, it is important that they are tilted within 30-40 degrees. Cooking is carried out from top to bottom. The electrode tip should be moved in one direction without any deviation to the sides.
About welding galvanized steel
This material is also called galvanized. Represents thin sheets of steel on which the zinc coating is applied. Before joining the edges, the coating is completely removed in this place of galvanization. This can be done mechanically using an abrasive wheel, sandpaper or a metal brush.
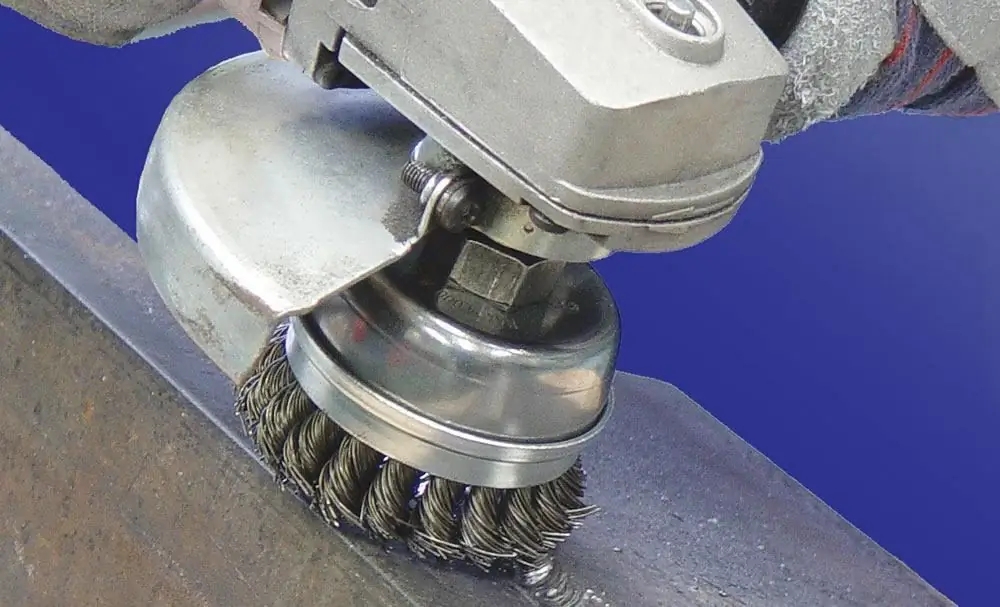
Not bad the coating is burned out by a welding machine. Due to the fact that zinc, evaporating at a temperature of 900 degrees, emits very toxic fumes, these works must be performed outdoors or in well-ventilated areas. After each pass with the electrode, you need to knock down the flux. When zinc is completely removed from the surface, you can proceed directly to welding. Galvanized pipes are mainly connected by two passes with electrodes of different brands. For the first pass, products containing a rutile coating are used. well yourselfrecommended electrodes OZS-4, ANO-4 and MP-3. During welding, they should fluctuate with a small amplitude. To form the upper facing seam, experts recommend using DSK-50 or UONI 13/55 electrodes. The area of the last seam should be slightly wider.