Horizontal directional drilling is one of the most popular methods of creating wells, which is used during repair work, laying communication lines under existing transport routes. When using this method of drilling, there is a slight destruction of the earth massif, which favorably affects its stability and bearing capacity.
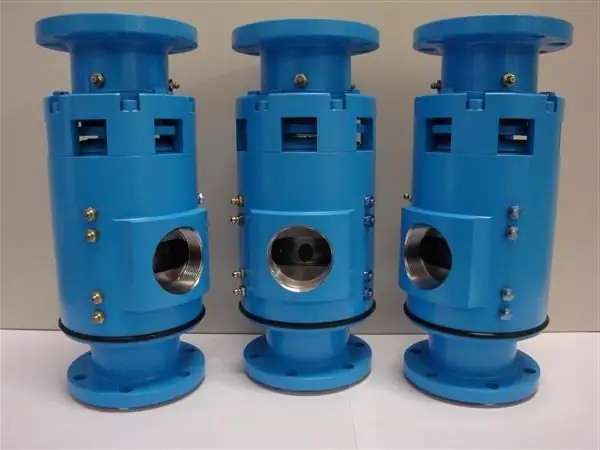
One of the main elements of the installations involved in the creation of both vertically and horizontally directed wells is a drilling swivel. Without this mechanism, it is impossible to carry out work on spot mining. Proper use of it allows you to get wells of the desired dimensions with an accuracy of 10 millimeters.
Destination
Any drilling rig consists of three main elements - traveling system, swivel and drill string. The traveling system is a supporting structure, which is pronounced when creating vertical wells. It performs the functions of moving drilling equipment,creates the force necessary to sink the equipment into the ground and is responsible for the stability of the entire installation.
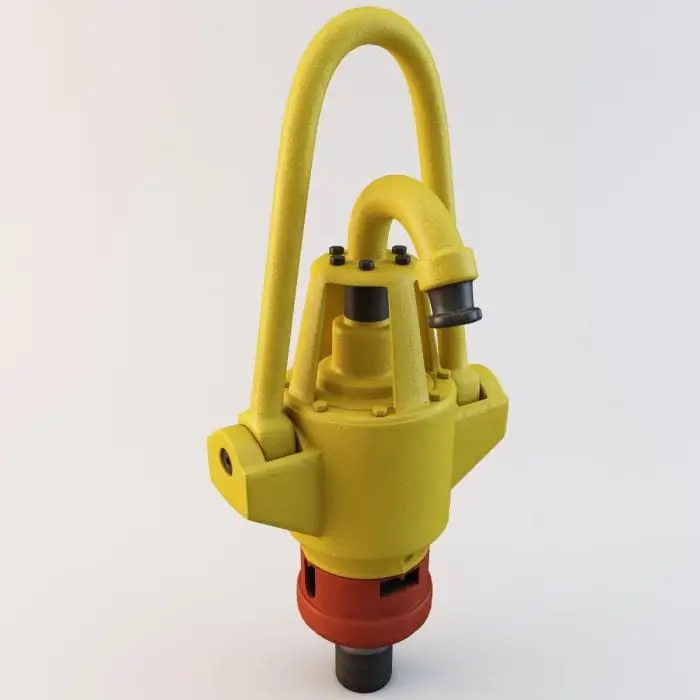
A rotor is installed on the traveling system, rotating the column (rod with a nozzle) with a drill for excavation. The drilling swivel is an intermediate link between these two elements. It is necessary to hold the weight of the drill string, supply flushing fluid and prevent twisting of the ropes. In horizontal directional drilling, the swivel is attached to the elevator links - a mechanism that connects the column to a device that moves the drill in a given plane. There are three main types of swivel - flushing, power and operational. Each type has its own characteristics.
Flushing swivel
The flushing drilling swivel serves to supply the solution to the excavation site. Structurally, it is an elongated hollow cylinder, which is placed in a streamlined metal casting, or body. The frame is attached to the rotor with a hinge, or the so-called earring.
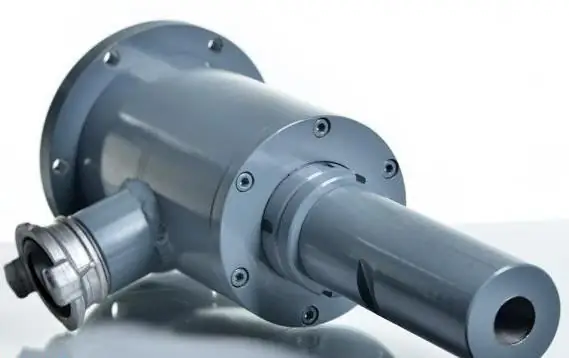
The body of the flushing swivel has a special outlet to which a hose is connected that supplies liquid. The solution, passing under high pressure through the hollow cylinder of the described device, enters the rotating column, and then into the face itself. The process of washing out the soil begins. The flushing, or bentonite, drilling plow is distinguished by the ability to transmit force through its body. Based on this indicator, installations for 20, 30, 50 or moretons.
Operational and power swivel
The power subtype of devices is used at the final stage of the drilling process. Its upper edge has rotational equipment and a drive. With their help, the swivel takes over the functions of the rotor, reducing costs and speeding up the creation of the well. Models of this subtype differ in power and type of docking element. The operational type of devices performs two functions at once - the creation of a rotational force (using a built-in device) and the supply of a flushing solution. You can perform any downhole work if you connect the drill string and the presented swivel. The drilling rig resulting from such a combination will not be inferior in performance to professional equipment.
Requirements for drilling swivels
Drilling swivel is nothing more than a connecting node designed to work in difficult conditions. It must maintain tightness when high pressure occurs in the circulation system of the drilling rig. In addition, it must endure alternating and unstable loads.
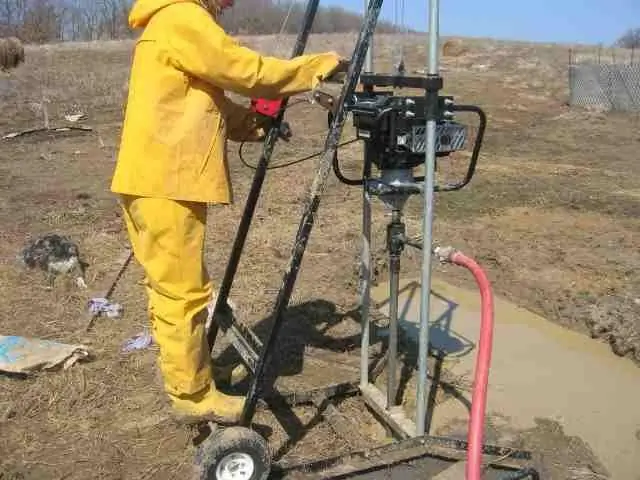
During the rotation of the drill string, both static overloads and dynamic stresses occur, which the rig must cope with. Moreover, the drilling swivel should have anti-corrosion protection and a special coating to improve wear resistance.
Features of choice
For effective and efficient drilling, it is important that the swivel meets all the requirements describedhigher. In addition, it must also meet the basic standards for this type of equipment:
- The transverse dimensions should not prevent movement along the tackle system during tripping, as well as the extension of the drill string.
- Coupling with the bearing block of the drilling rig must be reliable and convenient for dismantling the equipment after completion of work.
- Lubricant must be evenly distributed throughout the structure so that the small rig swivel does not overheat.
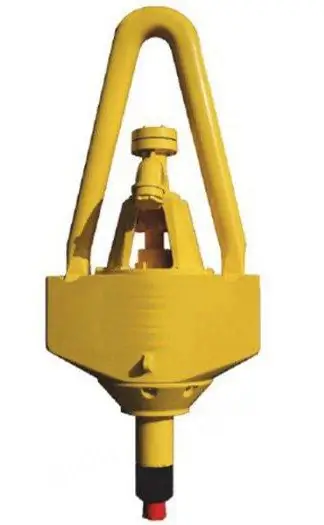
To increase the productivity of drilling operations, it is recommended to choose equipment whose constituent elements can be quickly and easily replaced in case of heavy wear. It is important to remember that the performance and service life of the entire drilling rig depends on the reliability and durability of the swivel.
Conclusion
Even if you plan to develop a well in your area, it is not recommended to assemble a drilling swivel with your own hands. This is a complex equipment, which is subject to increased requirements for wear resistance. The operation of the entire drilling rig depends on its durability and reliability, from the traveling system to the rotor, drill rod and drill. Special projects must be carried out according to drawings agreed with an experienced designer. They contain information regarding tolerances and treatments that will ensure long-term performance of the assembly, taking into account the performance of all elements of the drilling rig.