Semi-automatic installations always require slightly different equipment than "manual" or fully automatic devices. Steel and welding units are no exception. Many of them require a special semi-automatic burner. Such a device has several fundamental differences from its "manual" counterpart, which cannot be ignored when choosing and operating.
Semi-automatic burner features
Torches of semi-automatic welding equipment can be classified as consumables. Their average service life (with due regard) is no more than six months. The main difference between the specimens and the "manual counterparts" is the presence of a cooling system, as well as a welding wire feed mechanism.
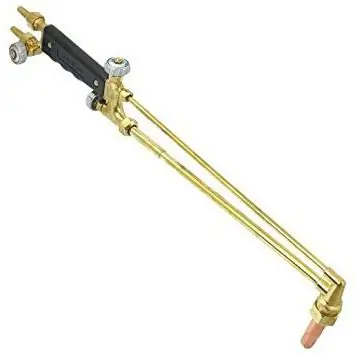
The ratings of the devices depend on the type of cooling, the type of connector for connecting to the welding machine and the welding current. The semi-automatic burner is actively used for work in hard-to-reach places. One of its key features is the way to protect the weld pool - the place where two metal surfaces join. This process is carried out without gas.
Design of semi-automatic burners
The torch generates a gas welding flame, in the jet of which the material melts.
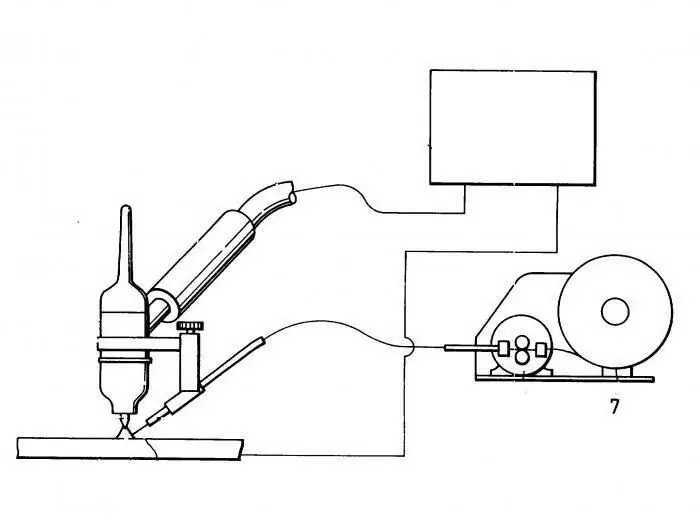
This task is solved by three main elements included in the design of the device:
- Train, or sleeve. The torch for the semi-automatic device is connected with the welding machine with its help, "receives" gas and wire during operation.
- The torch itself, which serves to communicate with the welding process, and also supplies wire, coolant, electric current and shielding gas, flux.
- The contact connection component connects the device to the welding equipment.
Directly, the semi-automatic torch includes a handle, a gas fitting, a uniform wire feeder and a tip in its design. The last element is made of various materials, but the most durable are tungsten or copper tips.
Features of maintenance of semi-automatic burners
A feature of the maintenance of welding torches is that their components need to be replaced periodically. The nozzle is the first detail that needs close attention. During welding of the material, droplets of molten metal remain on its surface.metal to be removed.
This can only be done mechanically, which leads to the appearance of microscopic cracks. It is because of them that the semi-automatic burner lasts about 6 months. But if you periodically change the nozzle, then this period can be doubled.

Contact elements are the second part of the mechanism that needs special attention. They operate in short circuit mode, which is why they heat up to a temperature close to critical and burn out. This leads to a decrease in their performance.
The average service life of these elements is about 200 hours of continuous operation. Usually they are included in the repair kit that comes with the burner itself. Detailed data can be found in the technical data sheet of the device.
How to save money when choosing a burner?
It is necessary to choose devices based on the requirements of welding equipment, as well as based on the expected scope of work and their complexity. But first of all, a welding torch for semi-automatic machines should be convenient, small in size and light in weight.
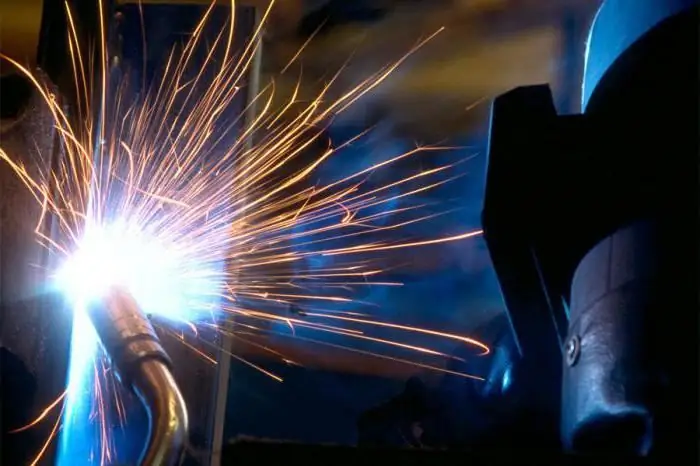
This can be achieved by choosing a device with a lower welding current than the semiautomatic device requires. You can do this for several reasons:
- The welding current specified in the documentation reflects the maximum temperature value above which the handle or cable will fail, but not the burner itself.
- Durability calculated at 100% loaddevices, which is extremely rare in practice.
According to the above, it can be concluded that a semi-automatic torch, mig for example, with a maximum current of 300A, can work without problems with a welding machine in which this value reaches 400 Amp.
Thus, by choosing a model with lower specifications, you will win in price and at the same time create optimal working conditions.