Gear reducer is designed to change the frequency and direction of rotation of the shaft. It transfers power from the engine to the desired machine unit, which operates on the principle of rotary motion. In any power unit, you can find gearboxes of different types, depending on their design and purpose.
Application of gears
The scope of application of gearboxes is wide - from mini-drives in medical equipment to power plants of factory value. They have found a place in agriculture, metallurgy, the coal industry, mechanical engineering, shipping and automobiles. Gear reducers are operated in different climatic conditions - indoors, outdoors, in heat, cold and even in arctic conditions.
The use of gear systems is due not only to the ability to change the direction of movement of the shaft. With the help of gears, the rotation speed increases and decreases, the torque on the shaft changes (more often increases).
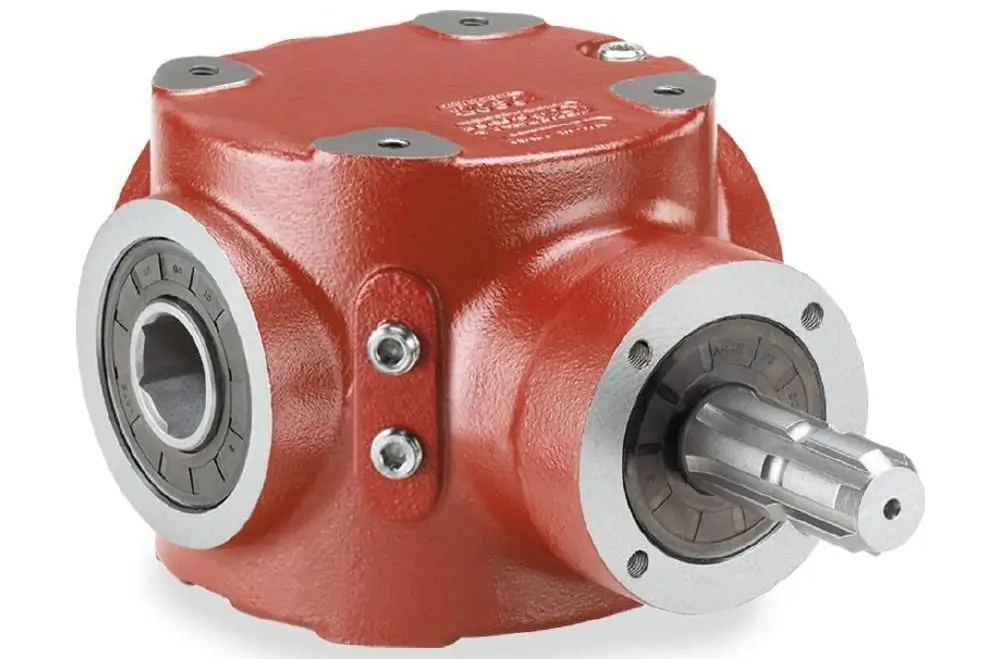
Classification by design
There are three types of gearboxes according to the principle of energy transfer - worm, wheel and wave. According to the type of layout and parts used, worm, chain and gear reducers are distinguished. Often there are hybrid options. Their design combines gears and chain drives at the same time.
Mechanisms based on gears are available in two types - with a cylindrical and bevel gear, depending on the shape of the working element. The latter transmit rotation at an angle of 90 ° relative to the axis of the engine.
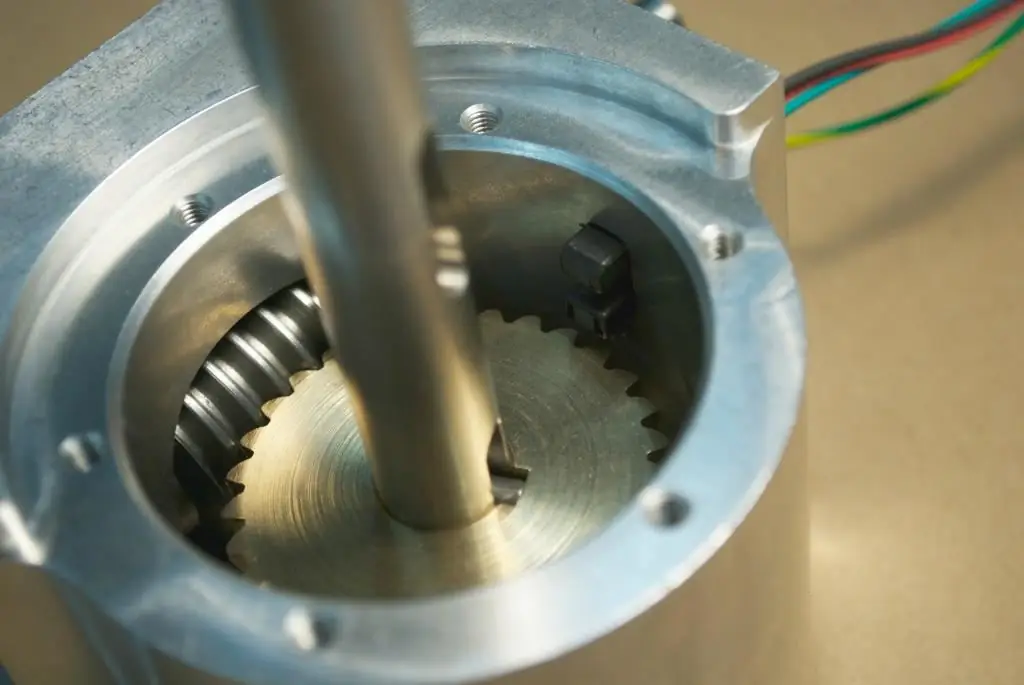
Design and features
The design of any gearbox is simple - it is a set of gears, shafts, bearings with a lubrication system installed in a common closed housing. Hybrid transmission devices are more complex - chains, belt drives, worms are placed in their housing. The system of gears and shafts makes up a gear train, and each pair of them in one housing determines the number of gear ratios. In gear chain reducers, the chain with two stars is an additional stage.
The main characteristics of any gearbox are its efficiency, number of steps and gear ratios. The efficiency depends on the ratio of power on the input and output shaft. Cylindrical gears have the highest efficiency, as they are the simplest with minimal power loss. The gear ratio is measured by the ratio of the speeds of rotation of the shafts at the input and output of the mechanism, and for each stage, own numbers are calculated according to the sameprinciple.
Combining gear pairs of different rotational speeds and their number in one housing allows you to obtain the specified characteristics on the output shaft - power, rotation speed and direction.
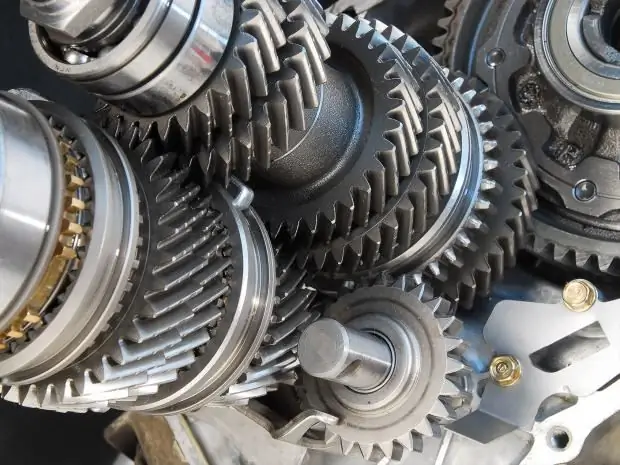
Features of the cylindrical device
Spur gear reducer is the most common type used in engineering, metallurgy and agriculture. Straight and helical gears are structurally simple and reliable, easy to operate. Its design, if necessary, becomes more complicated, becoming reversible - for use in cars or garden equipment.
Spur gear has 98-99% efficiency and low heat generation. At the same time, the gears are able to transmit high power to the target node of the mechanism.
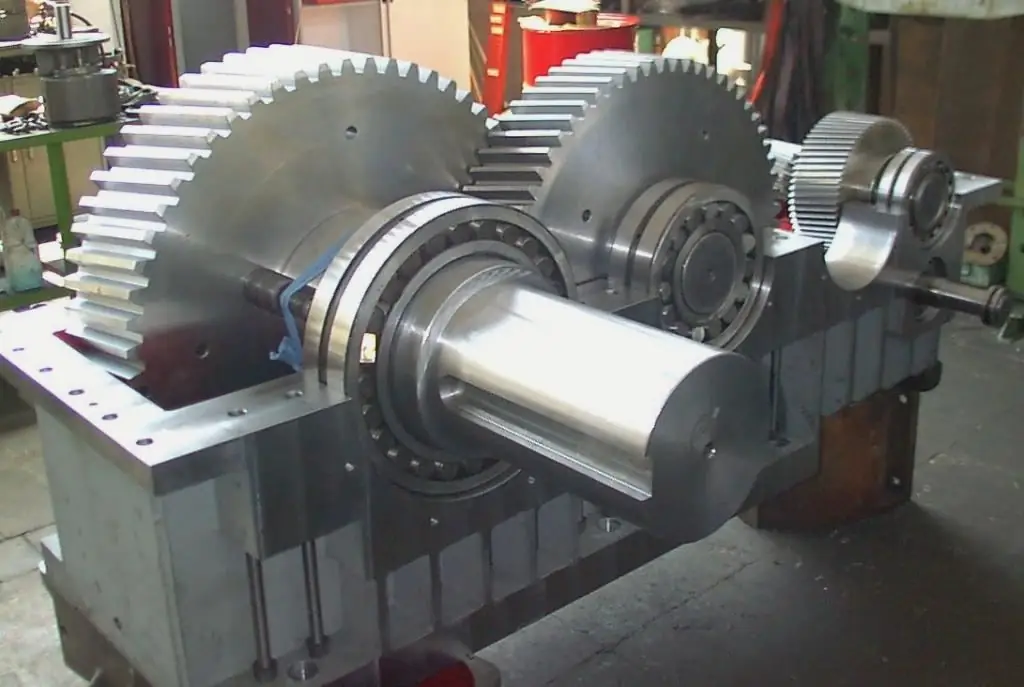
Spur gearboxes are available for both industry and private use. You can buy a separately sold gearbox and use it on any homemade device.
The disadvantage of the gear cylindrical device is the complexity of maintenance compared to chain drives of the same power and high noise during operation.
Home use
Gear reduction gear for low power devices (up to 10-15 horsepower), available in stores, is actively used in gardening equipment - in motor cultivators, seeders. Craftsmen involved in the mechanization of labor, with the help of purchased orhome-made gearboxes make walk-behind tractors for plowing the garden. This is one of the common applications of the gear unit in the household, apart from automobiles.
Motoblocks with gears
Motoblock with a gear reducer is designed for plowing and cultivating land of a small area. Depending on the size of the plot, the power of a mechanical plow is selected, reaching 10-15 liters. with. The operation of a mechanism of such power is impossible on a belt or chain drive. After all, gears can withstand much greater loads.
A reduction gear mounted on powerful walk-behind tractors can be made independently from spare parts of automobile differentials and gearboxes or bought at a store from a number of products for garden purposes.
Companies "Mobil-K" or CJSC "Krasny Oktyabr - Neva" produce gear spur gearboxes for the transmission of motor blocks of Russian assembly. These devices are produced as spare parts for cultivators, therefore they are not always interchangeable. This limits their installation on another model of walk-behind tractor.
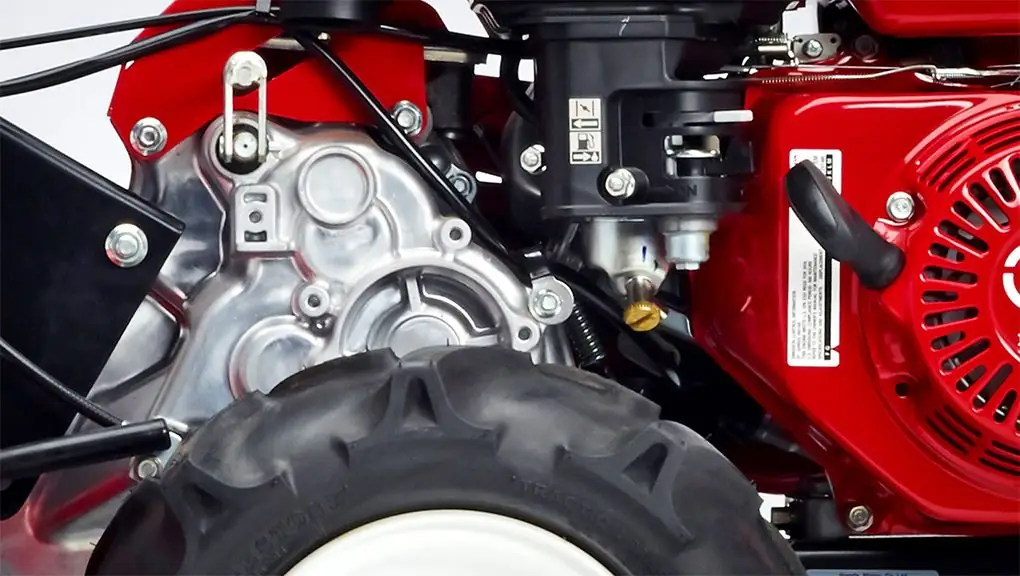
Motoblocks with a gear reducer and a disc clutch have gained popularity due to gear shifting without stopping the pulley. But such designs are more complicated and more expensive.
The most common are hermetically sealed oil-bath gearboxes with aluminum housings. Due to their low weight and simple design, such mechanisms practically do not require maintenance. There are non-separable models that, when exitingformations change and cannot be repaired.
Self assembly
Some gearbox models are sold at a high price - 11-18 thousand rubles, so garden owners often ask how to make a gear reducer in a home workshop.
For the manufacture of a handicraft transmission unit for a walk-behind tractor, you need a welding machine, a hacksaw, a hammer, pliers, an electric drill, screwdrivers and other tools. The components are shafts and gears of gearboxes from cars or old Soviet Druzhba-type chainsaws.
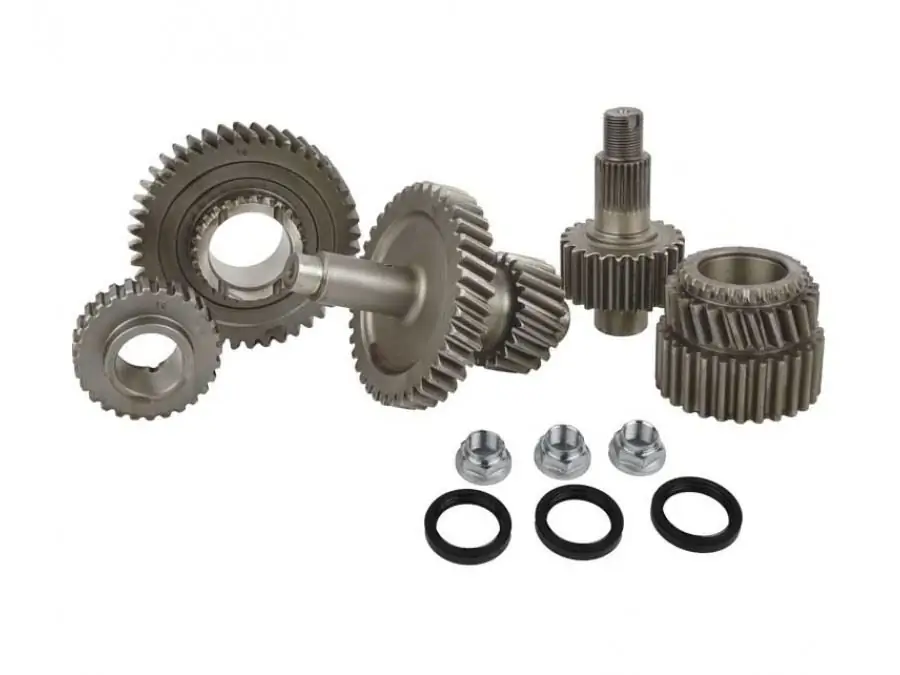
The most complex part of the gear mechanism is the housing. As a rule, borrowed components are incompatible with the gear housings sold for walk-behind tractors. In this case, there are two options - use ready-made housings from gearboxes or make your own from two thick plates with holes for shafts with bearings.
The body is marked along the axes relative to the assembled two- or three-stage gear and is prepared for pressing the bearings into holes reinforced with wide pins. Then the body is sealed and filled with oil. The output shaft of the resulting gearbox is connected to the walk-behind tractor pulley, and the input shaft to the engine.